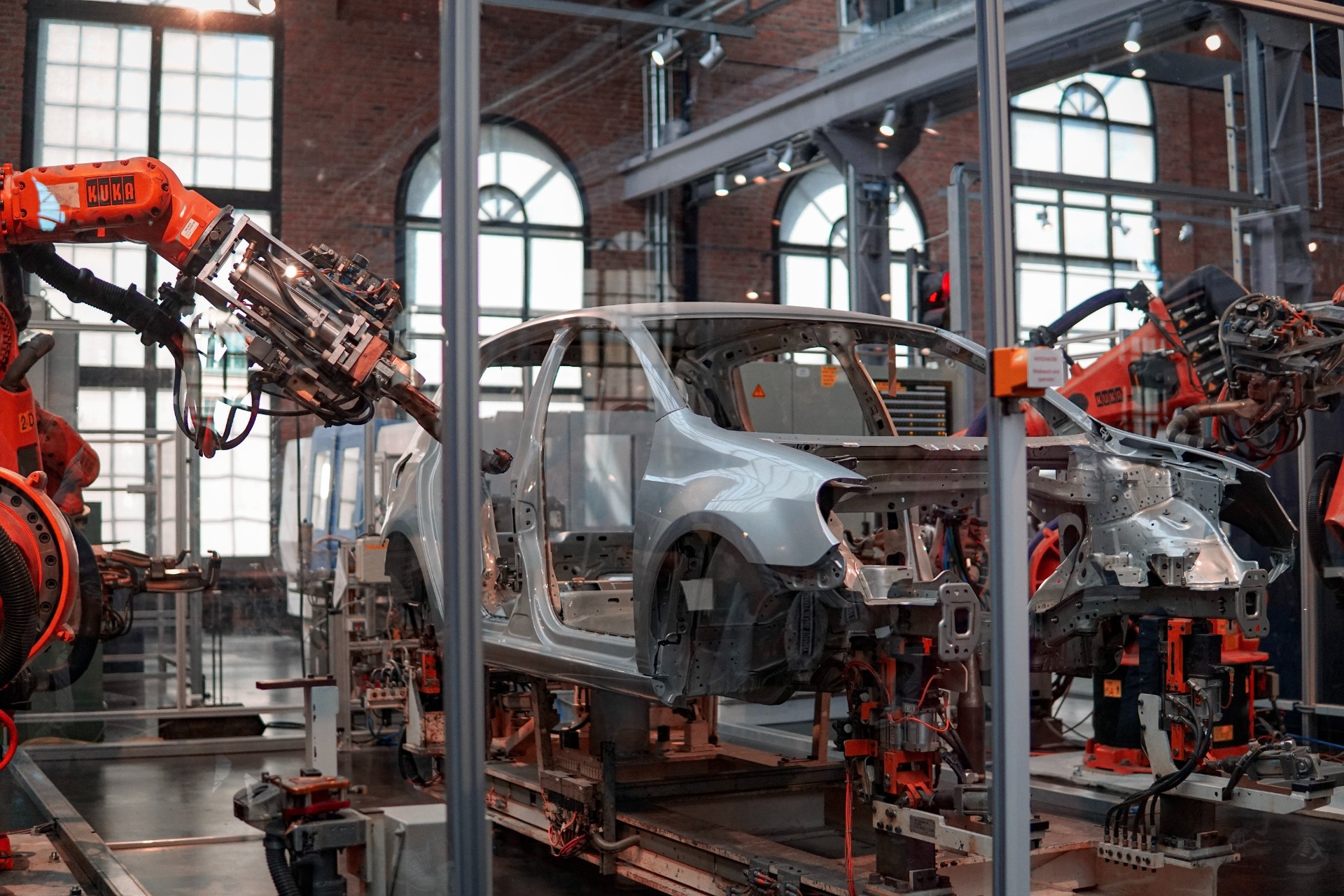
La industria automotriz y los próximos pasos de TESLA
La industria automotriz es una de las industrias más fascinantes. Mientras finalizaba mis estudios en Ingeniería Industrial tuve la oportunidad de hacer mis prácticas preprofesionales en la planta ensambladora de Nissan Motor del Perú, cuando aún producíamos vehículos en el país, hacia finales de los años ochenta. Estaba fascinada contribuyendo con el proceso de planeamiento, con la responsabilidad de revisar que todas las partes y componentes que se importaban desde Japón llegaran a tiempo y en la cantidad requerida para programar cada lote de producción.
Para mí, en esa época, era impresionante ingresar a la planta, ver el proceso de ensamble, su complejidad, cómo cada parte y componente iba formando parte de un vehículo, ver cómo se montaba la carrocería sobre el chasís, con todos los puntos de soldadura, para luego dar paso al montaje de los sistemas mecánicos, eléctricos y electrónicos, los asientos y el revestimiento del vehículo, todo ingresaba en forma sincrónica, con muchos operarios especializados armando los vehículos a medida que avanzaban en la línea de procesos.
En aquella época y en aquella planta, la mayor cantidad de autopartes se recibía desde Japón y las demás se fabricaban en Perú. ¿Qué hubiera pasado si una pieza no llegaba a tiempo? Hubiera sido un desastre, imaginemos por un momento un lote de cien autos sin poder ser terminados ¿Dónde ponerlos mientras llegaba la pieza faltante? y además los sobre costos asociados, los costos hundidos de mano de obra y gastos de fabricación, el incumplimiento en la entrega de los autos al cliente final, el impacto en los ingresos por ventas no realizadas y el impacto en la imagen de la marca, entre otros.
La industria automotriz ha ido evolucionando en el tiempo, se ha automatizado y desarrollado en un mundo totalmente globalizado, buscando eficiencias por economías de escala y centralizando la producción de los vehículos y de las partes y componentes en los países con los costos operativos más bajos. Así, hoy en día, una planta ensambladora ubicada en Colombia, por ejemplo, puede recibir una pieza de carrocería fabricada en Rumanía, formada sobre una plancha metálica elaborada en una fábrica metalúrgica de China, utilizando mineral extraído por una empresa minera en Australia.
Este sistema globalizado, que busca obtener el costo total más bajo, puede resultar muy complejo, con altos riesgos de suministro y además tener altos impactos sobre el medio ambiente por la cantidad de procesos de transporte involucrados a lo largo de la cadena de suministro.
Tesla, la marca de vehículos eléctricos de Elon Musk, uno de los hombres más ricos del mundo, planea masificar los vehículos eléctricos y para esto ha apostado por aprovechar las eficiencias de las economías de escala y la automatización, con el claro objetivo de ganar eficiencia y velocidad, reduciendo costos y acortando el ciclo de producción para capturar la mayor porción del mercado de autos eléctricos en el menor tiempo posible.
Qué distinto es el proceso productivo de Tesla comparado con el que tuve oportunidad de ver hace tres décadas atrás.
Actualmente, la planta de Tesla ubicada en los Estados Unidos es capaz de fabricar 5,000 vehículos semanales y está en proceso de expandir sus operaciones para llegar a producir un millón de vehículos anuales hacia el año en el 2030.
¿Qué diferencias existen entre la cadena de suministro de Tesla en comparación con otras marcas de automóviles?
Una de las diferencias más importantes es el nivel de automatización de la fábrica de Tesla. Como resultado, Tesla ha logrado tener un ciclo de producción de 3 días.
Una segunda diferencia es que Tesla ha incorporado el proceso de estampado de las piezas de la carrocería a línea de producción, evitando tener inventarios y evitando transportes innecesarios. El cuerpo del vehículo es armado íntegramente por más de mil robots autónomos, ingresando luego al proceso de pintura del vehículo.
Otra de las diferencias es que los sistemas que componen el vehículo son armados en paralelo, con lo cual se logra reducir el ciclo de producción a 90 minutos, una vez que finaliza el proceso de pintura.
Por esta razón, Tesla tiene el foco puesto en reducir los tiempos de traslado de los vehículos terminados desde la planta de fabricación hacia el mercado. En este sentido, una de sus estrategias es abrir centros de producción en otras regiones. Así, en el 2018 implementó una fábrica en China y espera construir una fábrica en Alemania en el 2021.
Pero estos nos son los únicos cambios que Tesla piensa hacer en su cadena de suministro. Un ejemplo muy interesante es la producción de baterías, uno de los componentes críticos para los autos eléctricos.
Actualmente, las baterías de los autos Tesla son fabricadas por Panasonic en la ciudad de Nevada, en los Estados Unidos. El litio, que proviene de Argentina o Australia, viaja hasta china para ser convertido en hidróxido de litio y, luego, viaja nuevamente hasta Sumitomo en Japón donde se fabrican los cátodos de litio y desde allí son enviados hacia los Estados Unidos.
El níquel tiene un recorrido similar. Probablemente, viaje desde Filipinas, New Caledonia, Indonesia, Rusia o Brasil, hasta la China para ser procesado, desde allí hacia Japón donde se fabrican los cátodos de níquel y, finalmente, viaja hasta los Estados Unidos para formar parte de las baterías.
Esta larga y compleja construcción de la cadena de suministro de las baterías tiene un efecto importante en el costo de transporte, además de la generación de emisiones de gases de efecto invernadero y polución.
Tesla anunció recientemente la construcción de su propia planta de procesamiento de litio y níquel para fabricar las baterías. Según las estimaciones de Tesla, se puede reducir hasta un 80% de los costos de transporte utilizando litio y níquel producidos en Norteamérica para ser procesados en una planta propia que piensan construir en los Estados Unidos.
Este es un ejemplo de cómo las empresas pueden repensar sus estrategias de cadena de suministro, en un mundo sumamente competitivo, para hacerlas más simples, más eficientes, más seguras, confiables y sostenibles.
*Ilustración tomada de: Unplash by lenny kuhne.
Sobre la autora del artículo:
Patricia Marañón
Ejecutiva Senior, con sostenida experiencia liderando cadenas de suministro, en empresas multinacionales relacionadas a los sectores de energía, oil&gas, industria y consumo masivo. Promueve la migración de la gestión de la cadena de suministro basada sólo en el costo hacia un enfoque sostenible.